Bridging Past and Future: Helical Technology Redefining Foundation Repair in AZ
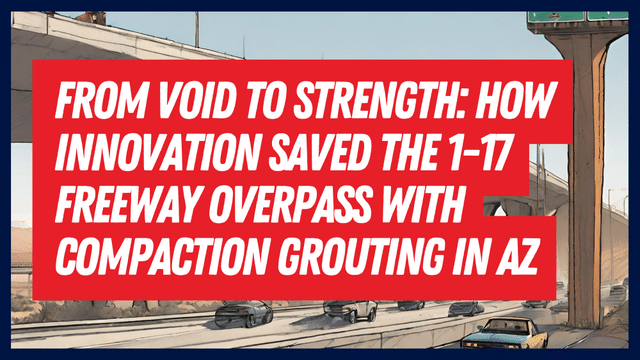
From Void to Strength: How Innovation Saved the 1-17 Freeway Overpass with Compaction Grouting in AZ
Introduction to Compaction Grouting and Pressure Grouting in AZ
In the realm of Foundation Repair, encountering challenges during construction projects is not uncommon. One such instance arose during the construction of a 70-foot-deep caisson intended to support the 1-17 Freeway overpass at Munds Park. Shortly after its construction, voids were discovered within the caisson structure. To address this issue, a meticulous repair process involving pressure grouting was initiated.
Investigating Voids and Preparing for Repairs
Upon discovering the voids at depths of both 14 feet and 70 feet, it became imperative to undertake a comprehensive cleaning process. Complications arose due to the caisson's location in an area with a high water table, facilitating the seepage of water and soil contaminants into the voids. To commence the repair, several core holes were drilled at the identified depths.
Utilizing Grout Pumps and Compaction Grouting Techniques in Arizona
Grout pumps played a pivotal role in the repair process, facilitating the injection of water and air into the core holes to clean the voids thoroughly. Moreover, specialized packers were installed atop the core holes to regulate the flow of water and grout. By strategically controlling the communication between the voids, thorough cleaning was achieved without compromising the stability of the surrounding soil.
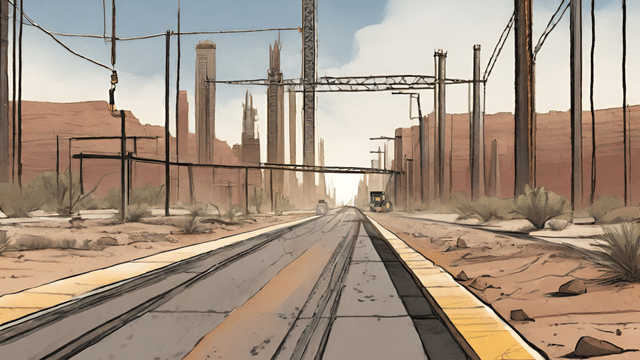
Implementing High-Strength Grout Materials in AZ
Given the caisson's location below the water table, selecting the appropriate grout material was crucial. The chosen grout material not only possessed anti-washout properties but also exhibited high strength, non-shrink characteristics, and excellent flowability. These properties were essential to ensure the integrity and stability of the repaired structure.
Executing Grouting Sequences and Ensuring Thixotropic Properties in Arizona
The grouting sequences commenced with the bottom void, followed by the middle void, employing a carefully orchestrated approach. It was imperative to maintain consistent pressure throughout the grouting process to prevent any delays or complications. Special attention was paid to the thixotropic nature of the chosen grout material, necessitating continuous pumping to prevent thickening within the ports or injection equipment.
Conclusion
Through meticulous planning and the application of advanced compaction grouting and pressure grouting techniques, the repair of the 70-foot-deep caisson was successfully completed within a tight timeframe. This undertaking serves as a testament to the ingenuity and expertise required to address unforeseen challenges in foundation repair projects, ensuring the safety and durability of critical infrastructure for years to come.