Grout Injection for Foundation Repair on Landfill Site Down in Arizona
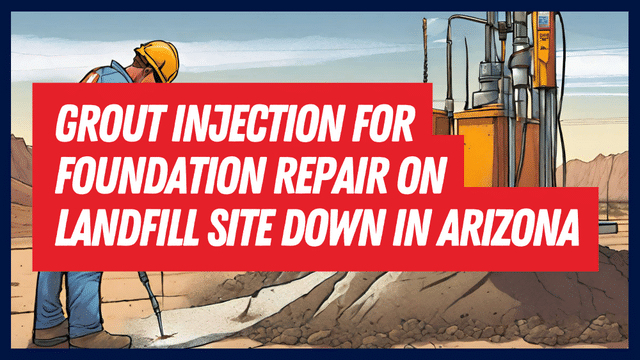
Grout Injection for Foundation Repair on Landfill Site Down in Arizona
Introduction
In the challenging world of foundation repair and soil stabilization, certain projects stand out due to their unique complexities. This article delves into a particularly challenging case involving a hotel built on top of a landfill with 10 feet of compacted fill, highlighting the use of grout injection, pressure grouting, and other innovative techniques.
Understanding the Problem
The landfill under this hotel presented a variety of issues, making traditional foundation repair methods impractical. Unlike typical soil conditions, this landfill contained not only concrete and steel but also decayed waste producing hazardous gases such as methane and hydrogen sulfide. Drilling into these conditions posed a significant risk, as injecting fresh oxygen could lead to explosive consequences.
Furthermore, the hazardous gases not only jeopardized the safety of the project but also posed serious health risks to the workers on-site. To address these challenges, an industrial environmental engineer was brought in to ensure the safety of the working conditions. Workers were equipped with gas sensors and emergency oxygen supplies.
The Solution: Compaction Grouting
Given the unique challenges of this project, the preferred method for stabilizing and re-leveling the foundation was compaction grouting. This technique involved injecting grout into the ground to compact the soil, improving its load-bearing capacity. To execute this method in a safe and effective manner, several steps were taken:
-
Casing Protection: To protect the casing used for grout injection from the percussive blows of the hydraulic concrete hammer, a custom-fabricated transition piece was employed. This ensured the integrity of the casing during the process.
-
Strata Verification: Before commencing the grout injection, a sonic boring was conducted to verify the strata at a depth of 50 feet, ensuring that the injection was precisely targeted for maximum effectiveness.
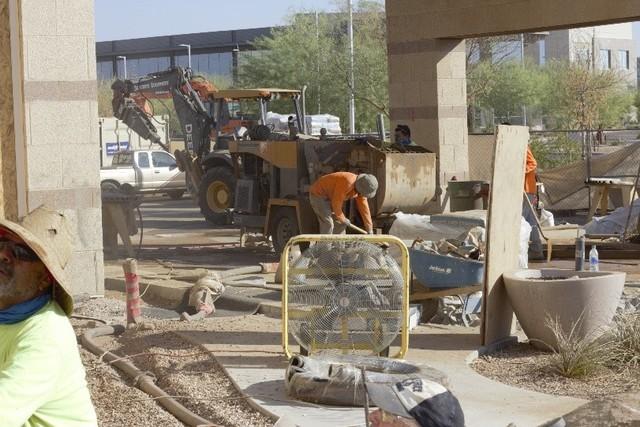
Adapting to Workspace Constraints
While the compaction grouting was a viable solution for the exterior of the building, the challenges continued as the project transitioned to the interior. The confined workspace did not accommodate traditional large excavators or sonic drill rigs. Instead, smaller excavators with compact hydraulic hammers had to be used.
In the initial stages of the project, a compact mini loader was employed to load sand and aggregates into the mixing hopper of the grout machine. However, as the project progressed, the need for a more space-efficient solution became evident. The team had to find innovative ways to work within the constraints of the interior space, making the project even more challenging.
In the forthcoming parts of this series, we will explore the intricacies of this project further, including the grout pumps, pressure grouting techniques, and the ingenious methods employed to navigate the confined workspace while ensuring the safety and success of the foundation repair endeavor. Stay tuned for more insights into this remarkable remediation project!